Batteries have reached a tipping point this year because silicon anodes are actually being produced and they do two things. They double the range of battery packs, and they allow incredibly fast charging.
First let me say that just about any advance in batteries involves some basic chemistry that was known decades ago. Lithium, Silicon, Sodium, and Sulfur were all identified as fantastic battery materials. However, the problem is always in the details. All of these have been experimented with, and it was just sheer luck that in the 1990’s Lithium-Ion cathodes and graphite anodes turned out the be the first big combination that worked well, and could be scaled-up to mass production at an affordable price.
For instance, even with the chemistry options set aside, we have been promised “Solid State Batteries” for over a decade. They actually exist in labs already, along with very expensive samples working right now on the International Space Station. The problem is in figuring out how to mass-produce large SSB’s, and to do it cheaply.
The majority of research during the early 2000’s has been on improving the positive Cathode, by tweaking the lithium chemistry with “NCM” which is Nickel, Cobalt, and Manganese. Great efforts have gone into reducing the amount of Cobalt used because it is rare, and much of it is mined under horrible conditions in Africa. Back in 2019, we wrote about how NMC532 cathodes (5% Nickel, 3% Manganese, and 2% Cobalt) now look like they would last 20 years of use (to see that article, click here). I noticed in the documents I researched, that this three-additive chemistry group is often called a “Ternary” chemistry.
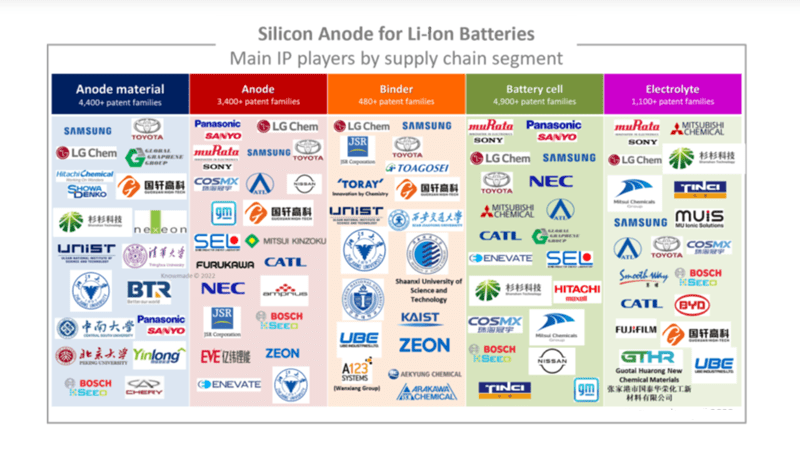
About ten years ago, a massive amount of money started to flow into research on the anodes of batteries, the “negative” electrode. This research is ongoing, but a few years back, silicon had a breakthrough, and now everyone is jumping on it, because the immediate effect is that the batteries are doubling their capacity, and charging times are shockingly fast (with future improvements being likely). The chart above represents thousands of patents that have been filed concerning the materials and processes that would allow silicon anodes to work.
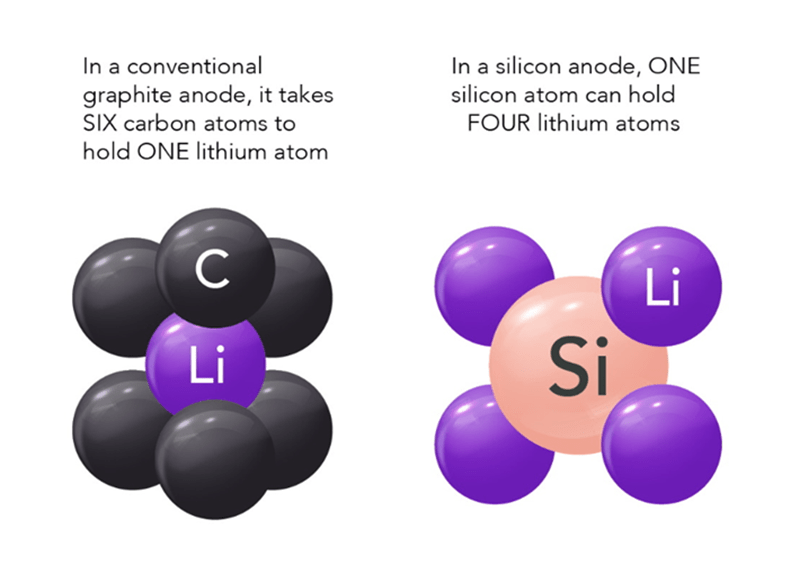
The graphic above shows why silicon, sodium, and sulfur are being heavily researched. They all hold a tremendous amount of potential for a dramatic increase of a packs range. And…if an economy EV only needed 100 miles of range, such a battery could be very small, light, and much cheaper. Sodium and Sulfur continue to be researched, but using Silicon in the anode is the big story for 2024.
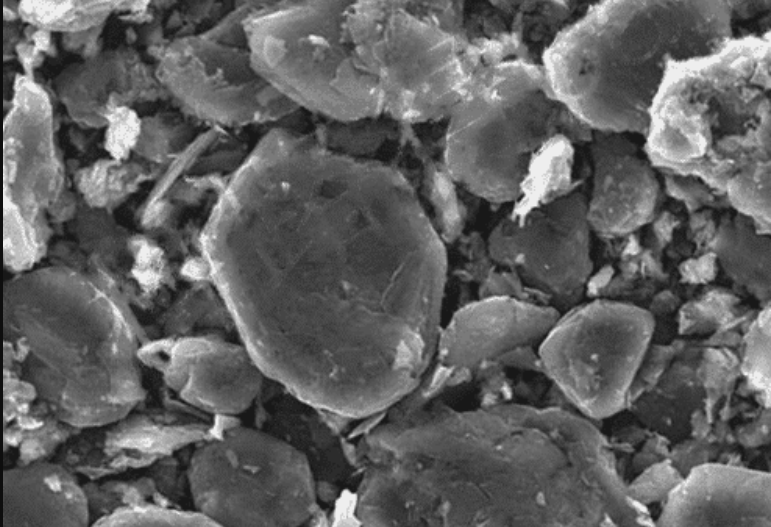
The pic above is an electron microscope image of a 90% graphite anode that has been infused with 10% silicon, from one of the early experiments. “In theory” this combination “could” increase the range of the pack, and it could be made using the existing cell-construction equipment. This is where the big problem with silicon in the anode raised its ugly head.
When a graphite anode is charged up, it can physically swell about 10%, which is manageable by using a thoughtful design of construction. The anode with silicon swelled to over 300%, and had a very short life.
Before I get into the two companies I want to highlight farther below, one common feature of the new silicon anodes is that they are thinner than the common graphite anodes. Graphite is a form of carbon that is relatively cheap and easy to acquire. For reasons I haven’t found yet, they are applied in a coating that is only about the thickness of a coat of paint, and yet the silicon anode material can be applied even thinner, as seen below. “Cu” is the elemental abbreviation for copper, and the copper thickness is roughly 1/4 of a millimeter.
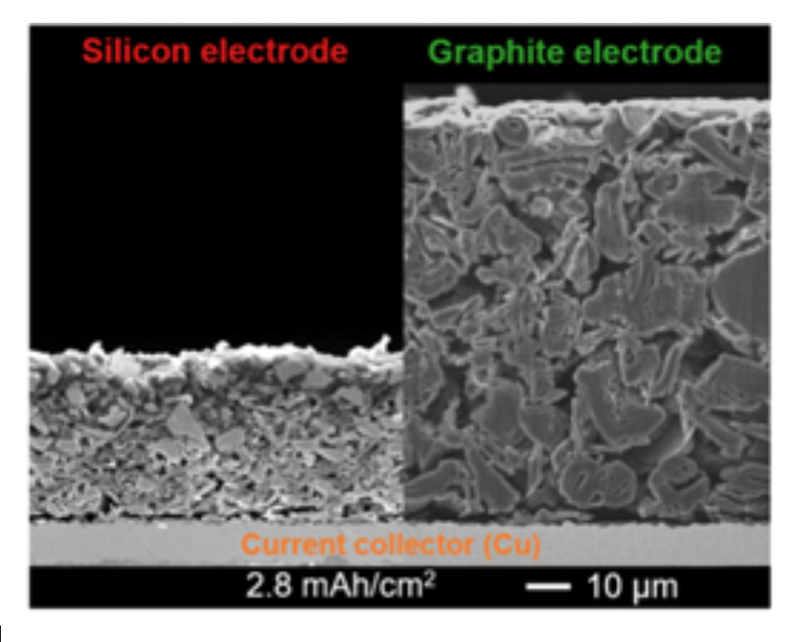
There may be several more ways to get silicon to work in an anode, but…that being said, lets get on to the two approaches I have found so far, from Amprius and Storedot.
____________________________________________
Amprius Technologies
This is is an American company based in Fremont, California. Founded in 2008 and based on technology developed at Stanford University. When their product was mature enough to begin producing it, Brighton, Colorado was selected for their manufacturing facility (North East Denver).
Both companies decided to tackle the swelling issue by creating a nano-scale silicon cage of sorts, that was built to be the size of the anode when it is swelled up, and for the lithium Ions to populate and then leave the spaces in their respective cages, during the charge and discharge.
Amprius developed a manufacturing process that causes silicon to build up on the collector as vertical “nanowires” like a microscopic forest of straight trees. The lithium Ions collect on the sides of the nanowires, like the bark of a tree.
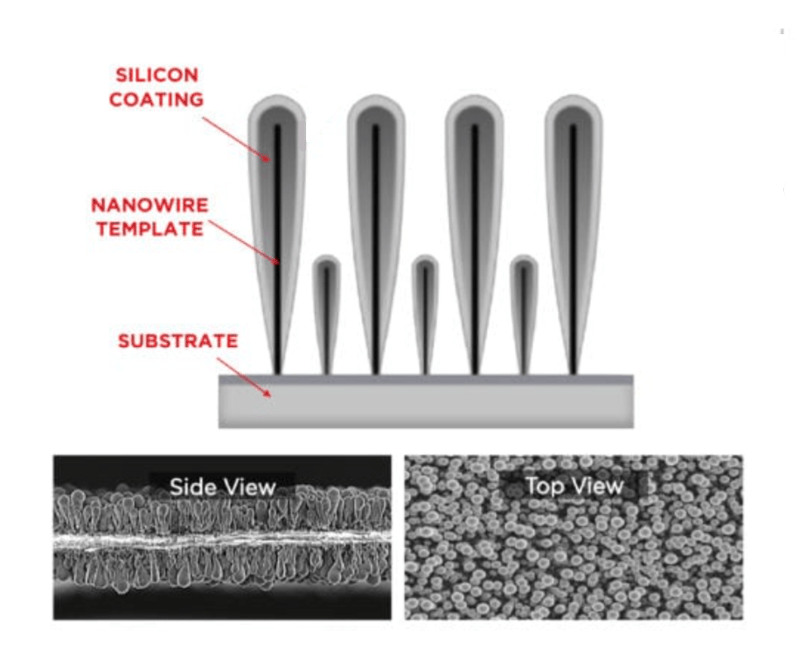
Since the majority of swelling would fill-in the available space sideways, the vertical growth was manageable. However, the silicon physical structure reduced the potential “spaces” of the anode, so rather than producing a theoretical quadrupling of energy per volume, initial version might only double the batteries range.
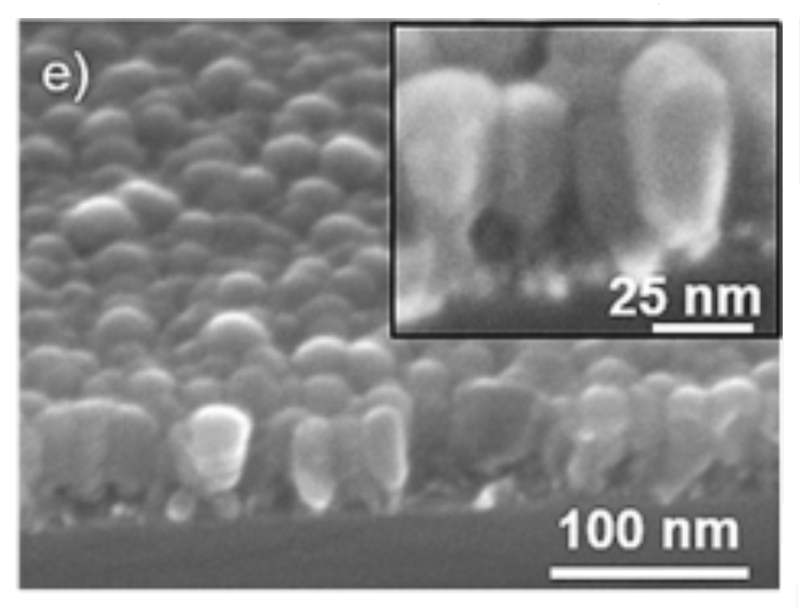
However, a promising avenue of research hopes to create a second layer of “trees” on top of the first layer.
If you haven’t heard much about Amprius yet, it “appears as though” the majority of their initial efforts are focused at securing military contracts, in spite of the huge market in the civilian world for EV cars, aircraft, laptops, cordless tools, and smart-phones.
____________________________________________
StoreDot
StoreDot was a small battery company back in 2012, with a focus on smart-phone batteries. However, they decided that the potential of using silicon in the anode of a lithium battery would be such an improvement, that they needed to invest in figuring out how to make that work. It was a big gamble, because you could spend years and millions of dollars to bring an idea to production, only to find that the problems were simply too hard to solve.
They came to the same conclusion as Amprius in that they made silicon cages with spaces that can hold and release lithium Ions. As much as StoreDot wanted to explore doubling the range in their batteries, their main focus was on rapid charging. Now that they feel that their tech is mature enough for production, they have also worked on scaling it up to automotive EV size, and they’ve stated that their “Extreme Fast Charging” can add 100 miles of EV range in five minutes of charging time. I am reluctant to use words like “amazing”, but there’s just no other way to describe that.

Now, this impressive battery uses a fairly conventional Cathode (positive electrode) of roughly 90% lithium-ion on a standard aluminum-foil ribbon-style collector, and the remaining material is “NMC”, meaning a fairly common additive set made from Nickel, Manganese, and Cobalt. StoreDot has stated that their particular chemistry uses NMC in an 8, 1, 1, ratio, meaning 8% nickel, and 1% each of Manganese and Cobalt.
The cathode (negative electrode) is a material that is applied to a copper foil collector. StoreDot has stated that the material is 40% silicon nanoparticles (with a small amount of Tin), applied to a base of graphene and graphite (both being carbon-based). The magic is in making nano-sized particles of silicon that are all the same size and shape (which is not easy), and attaching them in an even pattern, which results in a huge increase is surface area in the cathode. It may look smooth to the naked eye, but under a microscope, the increased surface area increases the energy capacity and also the speed at which it can be charged.
Several factors differentiate StoreDot’s product from other batteries. They have a patented highly porous ceramic-coated separator, and a solid electrolyte interphase layer made from a proprietary polymer. They are calling this their “Semi Solid State” battery. They had researched solid-state-batteries (like everyone else), but the roadblocks proved to be too difficult to fix, and the things they discovered along the way would lead them to this chemistry.
Their high energy density cells are being shipped in pouch format to StoreDot’s global automotive OEM partners for real-world testing, with a claimed 300 WH/kilogram and 700 WH/Liter. The cells exhibit the promised “100-in-5” charging performance, allowing drivers to charge 100 miles of range for each 5 minutes of charging.
These cells were repeatedly charged from 10% to 80% capacity in just 10 minutes and then discharged for one hour before recharging. The EV cells achieved more than 1000 of these extreme charging cycles consecutively before degrading below the 80% of the original capacity threshold. No noticeable degradation occurred within the first 600 cycles. The cells demonstrated a charge-rate of 4.2C, while they were discharged at an operating rate of 1C.
StoreDot further stated that they will be providing verification samples in both pouch form and the 4680 cylindrical cell. Their silicon-dense anode is also compatible with the Lithium-Iron-Phosphate / LiFePO4/LFP chemistry, which is popular in China.
StoreDot is based in Israel, and they have contracted with Eve Energy in China to produce their batteries. Their batteries were impressive enough that PoleStar, Daimler, Geely, and Volvo have already signed contracts with StoreDot.
____________________________________________
Written by Ron/spinningmagnets, July 2024
OK, so…the article is finished, and the signature and date have been added. So, why am I still writing here? I thought a few of our readers might be interested in why it took so long to figure out how to get silicon to work on an anode. There have been literally thousands of experiments that take time, effort, and money to set up. Since entirely new processes were invented (with many failures along the way, meaning the next experiment needed an entirely new machine and new process to see if THAT worked better) a lot of chemistry theory and creativity had to be harnessed.
Below is a few random paragraphs (in no particular order) that I found when I was researching why silicone anodes worked better, and how silicone anodes were created. Maybe just read the first few sentences, and understand that the rest sounds very similar…
White paper on silicon vaulted columns in lithium-ion battery anodes
“All samples were prepared using a gas-phase deposition system (Mantis Deposition Ltd) at high vacuum (2.0 × 10−8 mbar), supported by a rotatory holder (2 rpm for all depositions) to yield homogeneous film deposition. For Ta nanoparticle deposition, Ar gas flow of 60 standard cubic centimetres per minute, DC magnetron power of 45 W and aggregation zone length of 100 mm were selected. The silicon thin film was deposited with a 110-W RF-sputtering source, using an Ar pressure of 2.1 × 10−3 mbar. The magnetron sputtering targets, silicon (n-type, purity > 99.999%, resistivity < 0.001 W m) and tantalum (>99.95% purity), was purchased from Kurt J. Lesker. All depositions were performed at ambient temperature (~298 K, as measured by the substrate holder thermocouple), and with no external bias applied to the substrate. Finally, all copper foil anodes (0.25-mm thick) were annealed at 150 °C for 60 min at Ar pressure of 8 × 10−3 mbar…In the first group, we simulated the deposition of the silicon layer with and without the nanoparticle scaffold. Initially, an amorphous-silicon substrate was prepared by a fast heating (3000 K for 100 ps)–quenching (500 K for 100 ps) process in the isothermal–isobaric ensemble at 0 bar. The size of the thermalised simulation cells was 109 × 109 × 55 Å initially. Next, we opened the top surface and fixed an atomic layer within 6 Å at the bottom, and performed additional relaxation for 50 ps in the canonical ensemble. For the structure with the nanoparticle scaffold, the nanoparticle was deposited on the amorphous-silicon substrate naturally. We placed a diamond-lattice silicon nanoparticle 5 nm in diameter at 15 Å above the surface at the (0, 0) position laterally. The silicon nanoparticle was thermalised at 500 K for 50 ps and was next given an additional velocity of 20 m/s so it would land on the substrate, where it was allowed to relax for another 50 ps. Film growth was simulated by adding a new silicon atom from the top of the cell every 200 MD steps; 215,563 silicon atoms were added in total (at an average deposition rate of 1.1 nm/ns). In order to mimic the rotating substrate of the experimental setup, the initial velocities of the deposited atoms were set to rotate at a rate of 1 round/ns, performed in 20-ps steps. The angle of incidence was 30° from the surface and the total velocity was 1000 m/s. No scaling of velocity was applied to the non-deposited atoms. The temperature of the deposited atoms (except those fixed at the bottom) was controlled by applying a Langevin thermostat56 to the group of deposited atoms located 1 nm below the open surface. This group was updated every 2.8 ns, so the atoms deposited during that period were scaled after the update. The simulation was carried out for about 40 ns with a time step of 1 fs. We also performed benchmarking simulations with different nanoparticle and cell sizes and temperatures, or with two nanoparticles explicitly following the same procedures as described above…”
“…Si-based anodes are a promising alternative to graphite for high-energy LIBs because of their up-to-tenfold increase in theoretical capacity…A columnar amorphous-silicon film was grown on a tantalum-nanoparticle (TaN) scaffold due to its shadowing effect…The matrices used (usually of carbon or of polymeric nature) play a dual role: they connect electrically and physically the silicon components (typically nanoparticles of sizes below their break-up limit), and provide a steady electrode–electrolyte interface, enabling the formation of a stable SEI…First, crystalline Ta nanoparticles were deposited (Fig. 1a, step 1), forming a porous nanoparticulated film that acted as a nano scaffold (denoted TaNS)…Sample 54V presents columns of increasing diameter, resembling inverse truncated cones that touch at the top, forming a vaulted structure as shown by cross-sectional scanning electron microscopy (SEM, Fig. e)…E increases with film thickness until the columns touch each other forming multiple arches… a second TaNS is deposited on top of an existing silicon vaulted structure, followed by further silicon deposition…thus increasing the total amount of silicon in the anode…”
“…The vaulted nanoarchitecture presents possibilities for new designs in silicon anodes for LIBs, showing enhanced performance in terms of capacity retention, charge–discharge rate and Coulombic efficiency. More importantly, the fabrication strategy allows the vertical repetition of this nano-structural unit, demonstrated with the construction of a double-layer aqueduct-like structure that retains the structural and mechanical features of the single layer, but improves capacity retention and Coulombic efficiency while doubling the amount of silicon in the anode. In summary, the vaulted structure is a platform that can be piled up increasing the total amount of silicon, thus forming the basis of silicon anodes with sealed surfaces for stable SEIs and inner cavities that partly accommodate volume changes and mitigate stresses…”
“…The specific energy of silicon anodes is theoretically 4200 mAh/g, which’s over 10 times greater than lithium ion batteries with graphite anodes, which have a specific energy of 372 mAh/g…”
I could add more scientific gibberish, there’s a ton of these on the web. Just trust me that the silicon anode is the big driver right now for battery improvements.
.
.
.
#Silicon #Anodes
Source link