Agnius is from Lithuania, and he is best known for developing the N.E.S.E. battery pack building system. He recently build a longtail cargobike frame from scratch, and it had a few features that caught my eye. So let’s take a look.
______________________________________________
N.E.S.E Battery Modules
We wrote about the N.E.S.E. battery system in 2017, and that article can be found if you click here. The idea is that anyone from around the world could use a 3D-printer (or hire a local 3D service) to make the plastic housings in any size or color that you want. There is no soldering or welding required, the cells are held onto the buses by compression.
The parts that N.E.S.E supplies are the nickel-plated copper bus-strips, the threaded battery-posts, and the closed-cell rubber compression-foam backing that is made from Poron. The black Poron foam acts as a spring to maintain compression, and to take up any heat-expansion in the cells. If the foam was “open cell”, it would be like a kitchen sponge that water could pass through, which would lose its compression return-ability rapidly. Poron is a closed-cell material, so each one of the millions of tiny air bubbles that are trapped in it are sealed away from each other, and this type of foam will never lose it springy-ness. Link provided at the bottom of this article.
______________________________________________
The Longtail Cargobike
No matter what material you want to use, a long cargobike will be heavy, especially if you are going to add an electric drive system to it. So, most builders usually concede that its worthwhile to use a steel frame, for the ease of welding together the parts from several donor-frames (in the pic below, Agnius also used steel tubes from bedframes). Once that decision is made, steel frames can often be sourced for free by simply keeping an eye out for several months, to grab the old bike frames that are sitting on the curb for trash-day. And that is just what Agnius did.

If you read through the build thread (see link at the end), Agnius tried a 26-inch wheel on the front at first, with a 20-inch wheel in the back. Almost immediately, he changed to using 20-inch wheels on both the front and back. Doing that made the bike slightly lighter and shorter. In fact, if you do not intend to ride on roads with big potholes, the smaller 20-inch wheels are stronger than the larger 26/27.5/29’r wheels.
Agnius wanted a large multi-use tub behind the seat, similar to the Madsen cargobike (click here).

The pic below shows the pinching torque-arms for the direct-drive hubmotor axle in the rear drop-outs. As the powered rear wheel tries to turn forward, the axle is trying to turn backwards. The axle is affected by as much force as the wheel, so 1500W of peak power is trying to break or spread-out the frame drop-outs. These torque-arms will be welded over the drop-outs to add enough strength to prevent any problems.

As far as which power system to use, my “go to” suggestion for a cargobike is a BBSHD mid-drive using 52V and a small chainring (1500W stock, and 2500W with the Luna Ludicrous upgrade). Alternatives come and go, but that system continues to impress me, year after year. However, part of the appeal of Agnius’ build for me is that he is using a rarely-used configuration that I like a lot. Its a 1500W direct drive hubmotor in a small-diameter wheel.
What’s so great about that? Give me a minute to explain. The most common wheels (in inches) are the 26/27.5/29’r diameter. The larger-diameter wheels can roll over unexpected potholes with less of a jolt, so they can smooth-out a rough ride. However…the larger the wheel-diameter, the slower a hubmotor will spin when traveling at average speeds. Using low-RPM’s in a hubmotor which happens to be drawing high amps (from a heavy load) will cause the hubmotor to overheat.
If you try to use a geared hubmotor, it allows the internal motor to spin five times per hub rotation, so its efficiency is better than a direct-drive hubmotor. Geared hubmotors are the most popular drive for “general purpose” ebikes, since they cost less than most mid-drives, and are more efficient than direct-drive hubmotors. However…unfortunately for a heavy cargobike, a geared hubmotor has a poor heat-shedding path from the central hot stator to the outer aluminum shell…
And this brings us back to direct-drive (DD) hubmotors. If they are under-sized for the load, they can also overheat, but now…we have a much better selection of hubmotor sizes to choose from (click here for our article on hot-rod hubmotors). With a direct-drive, the motor spins at exactly the same RPM’s as the wheel, and a common 26-inch wheel will be spinning at only 260-RPM’s at 20-MPH. However…if you swap that same DD hubmotor into a smaller 20-inch wheel, the RPM’s go up to 336-RPM’s at 20-MPH (76 more RPM’s), which is a 30% improvement in wheel-torque and heat-reduction.

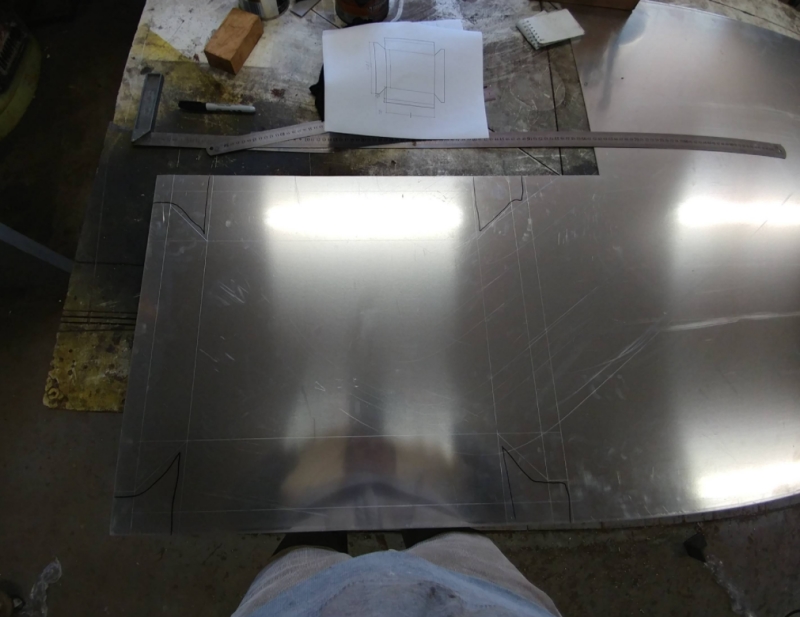


The large red block on the top right is the battery pack 20S / 6P (72V). The red box on the bottom left is the controller. The small clear box on the bottom right is the main fuse, and the small gray box at the top left is the 72V-to-12V DC/DC converter.



______________________________________________
Big DD Hubmotors in Small Wheels
The most common and affordable DD hubmotors use a 28mm wide lamination stack (forming the core of the stator), and they are typically advertised as a 1000W hubmotor. Most Chinese hubmotor manufacturers use a 35mm wide stator for their “1500W” DD-hubmotors. The added width of these motors will provide more torque, so heat is reduced because it doesn’t “bog down” as much. The 1500W rating is for continuous power, and these have taken 2600W as a temporary peak (52V x 50A). Swapping a 1500W motor from a common 26-inch wheel into a smaller 20-inch improves the hill-climbing torque and cooling a full 30%…
If a 35mm-wide stator in a 1500W DD hubmotor interests you, but you don’t already have a preference…the Leafbike brand (click here) seems to be popular. It uses the thinner 0.35mm laminations, instead of the common 0.50mm lams. That means that it will have less eddy-current “waste heat”, which is where battery watts are converted to heat, instead of work.

Back in 2015, we wrote about using a moped rim on a DD hubmotor (click here), and that is what I recommend for projects similar to this. The reason is because the moped rims use “angled nipple holes” (which is also the name of my band), and a regular bicycle rim will force the spokes to bend sharply right at the nipple. If you use a “one cross” spoke pattern (seen in the pic above), instead of a radial pattern (please don’t use a radial pattern, I’m asking as a friend), you will have fewer spoke breakages. Skim the article link I provided to see all the details why.
Moped/motorcycle rims and tires are measured differently than bicycle rims and tires. A 16-inch moped rim is 16-inches at the rim OD, which is the way they should be measured. A 20-inch bicycle tire is roughly 20-inches in diameter at the OD of the tire, but only when using the common average tire from 40 years ago (20-inch fat tires now exist). The majority of the so-called “20-inch” bicycle tires will seat properly on the rim of a 16-inch moped wheel (and vice versa). A 16-inch moped rim is roughly the same price as a heavy-duty BMX 20-inch rim, but the moped tires are surprisingly affordable, along with being very puncture resistant to avoid flats, and also very long lasting (please read the article in the link above!). For this job, I would use a moped rim and tire.

I really like the idea of having a 20-inch wheel on the back of a cargobike, since it puts the weight of cargo three inches lower than a common 26-inch rear wheel.
If you live where you’d be forced to roll over any unexpected potholes in the street, I’d recommend adding a suspension seatpost (click here), like a Cane Creek Thudbuster or a Suntour NCX. I’d also add a front suspension fork plus a 26-inch wheel on the front if your roads are bad, but…for well-maintained streets that are smooth, a solid fork is simpler and lighter, along with a 20-inch front wheel being slightly shorter and lighter.

Either way, for any serious street commuter hauling heavy cargo, I’d definitely recommend a large hydraulic disc brake on the front (click here to read why). Using a common rim V-brake can be adequate on the back (with upgraded pads like Kool-Stop), but…if there is a mount for a disc brake caliper, I’d prefer using discs, even if it is just for an average diameter disc with a cable actuated caliper, like the popular Avid BB7’s (common brake disc diameters are 160, 180, and 200mm).
______________________________________________
The Final Result
As you can see, Agnius is a capable guy who doing some creative and fun stuff. Thanks for reading this far, and I’d recommend that you go out and have some fun with ebikes…you wont regret it.

______________________________________________
Links
His longtail cargobike build discussion can be found here.
His website address is “18650.lt” (the suffix is “dot L-T”, for Lithuania), and you can check it out by clicking here.
______________________________________________
Written by Ron/spinningmagnets, June 2021
Source link